马上注册,结交更多好友,享用更多功能,让你轻松玩转社区。
您需要 登录 才可以下载或查看,没有账号?立即注册
x
1.催化裂化装置原理
方钉文库 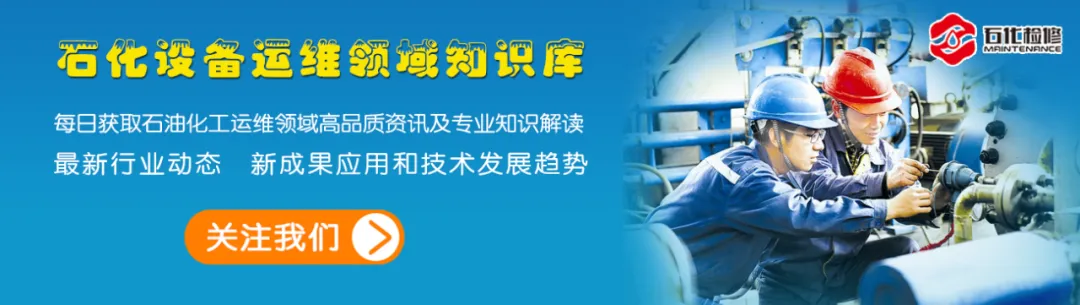 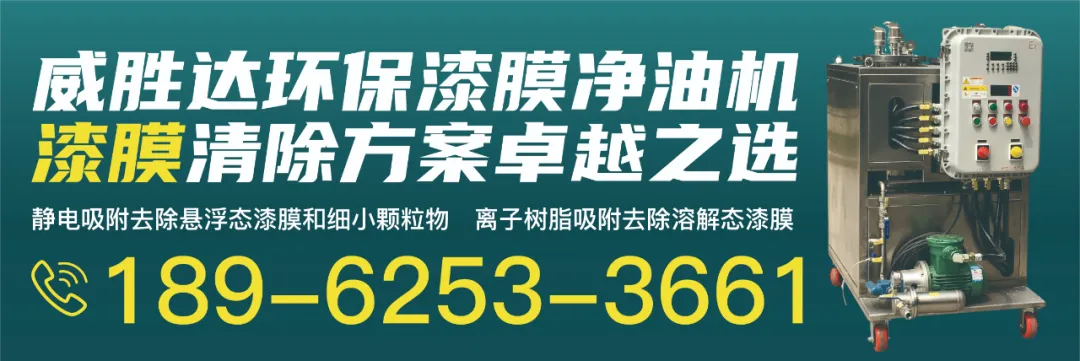 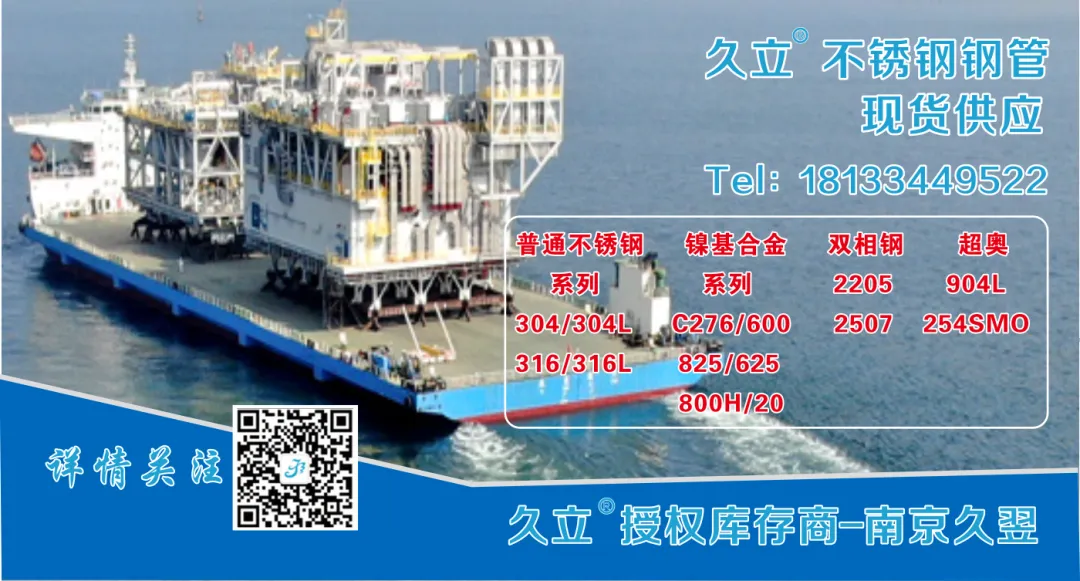 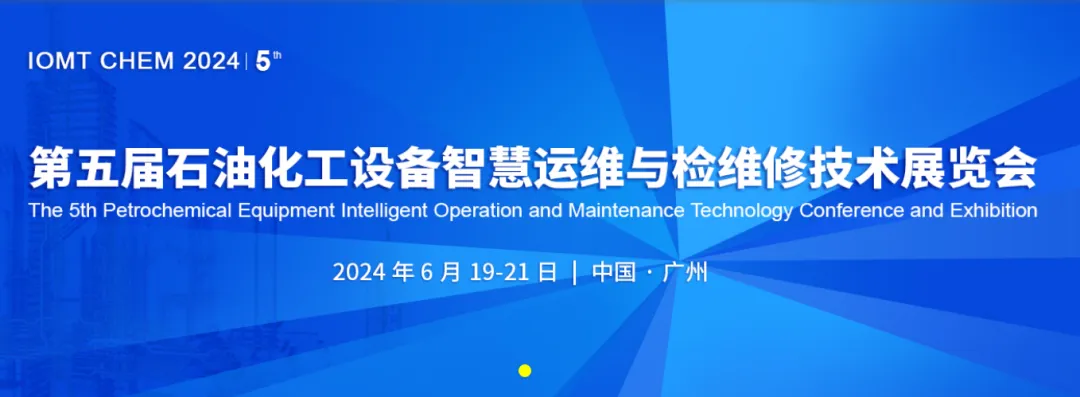
2.催化裂化装置流程图
致敬不凡,致敬平凡
3.催化裂化装置故障处置研究
摘 要:对中国石化在役催化裂化装置近三年非计划停工故障进行了统计分析,结果显示:静设备原因造成的非计划停工占19.64%,主要影响因素有反再内构件磨损老化及开裂、高温烟道及膨胀节应力开裂、低温部位腐蚀泄漏、特阀故障等;动设备造成的非计划停工占19.64%,主要影响因素有大型机组叶片断裂、转子失衡、不对中、喘振等。
4.催化裂化装置工艺流程
根据分析结果,提出了加大关键部位检维修深度、构建可靠性数据库、研发设备在线智能预警技术等措施,提高装置长周期运行水平关键词:催化裂化装置 非计划停工 磨损老化 低温腐蚀 早期预警流化催化裂化装置是炼油企业的核心装置,其在炼油企业的物料平衡、热量平衡、燃料平衡及油品质量升级中具有不可替代的作用。
5.催化裂化装置工艺流程图
中国石化在役催化裂化装置产能占全国总产能约40%炼油产业转型升级要求催化裂化装置向原料重质劣质化、安全长周期运行等方向发展然而,催化裂化装置工艺及设备结构复杂、操作条件苛刻多变【1】、腐蚀介质分布较广,装置的长周期运行面临诸多挑战。
6.催化裂化装置有哪三大系统?叙述各系统作用
统计2018~2020年中国石化炼油装置非计划停工情况发现,催化裂化装置非计划停工占比40.87%,是发生非计划停工最多的生产装置1 非计划停工总体情况2018~2020年,中国石化在役催化裂化装置静设备、动设备、电气、仪表、工艺、操作等6个方面均有造成装置非计划停工的案例,其中动、静设备原因占比均达到19.64%,如表1所示。
7.催化裂化装置的三器包括
表1 2018~2020年中国石化催化裂化装置 非计划停工原因统计
8.催化裂化装置 视频教学
2 静设备故障分析2.1 反再内构件磨损老化2.1.1 再生器翼阀磨损跑剂2019年7月20日,G公司3号催化裂化装置停工处理烟机振动超标问题,反应喷油恢复进料后发现再生器出现跑剂现象,装置停工检查检查发现,待生套筒流化风环磨穿开裂,4组待生催化剂分配器输送风管以及套筒内立管的密度测量点、松动点断裂,再生器一级料腿防倒锥脱落1支,如图1所示。
9.催化裂化装置 视频讲解
图1 待生套筒流化风环磨穿开裂情况再生器跑剂的主要原因是催化再生器内部结构复杂,开工过程尤其是转剂阶段,再生器密相床层不稳定,催化剂分布不均,产生偏流,造成一级料腿防倒锥脱落、待生套筒流化风环磨穿、待生剂分配器输送风管断裂等问题,从而导致再生器跑剂。
10.催化裂化装置 校审提纲
故障部位修复后,要强化平稳操作和设备维护,防止催化剂偏流等异常工况出现,杜绝非计划停工带来的次生事故2.1.2 VQS来油气管垂直段膨胀节泄漏2020年10月10日,D公司沉降器顶提升管VQS来油气管垂直段膨胀节发生泄漏,装置停工处理。
该膨胀节导流筒与膨胀节筒体间塞满不锈钢丝和硅酸铝纤维的隔热层,导流筒开口处有隔热枕,下方有挡环,挡环与导流筒之间留有波纹管的压缩间距结合之前检修时检查出的挡环冲刷磨损情况判断,油气夹带催化剂可能在冲击到挡环后返回,由于隔热枕的密封作用减弱,导致油气及催化剂进入隔热层内,并在内部形成涡流,不断冲刷波纹管,最终导致穿孔。
针对该问题,可采取以下应对措施:1)波纹管带压堵漏密封;2)重新对该处压力平衡型膨胀节进行设计计算,制作、更换新膨胀节2.1.3 烟机入口膨胀节导流筒焊缝开裂移位2020年4月23日,S公司1号催化裂化装置烟机入口膨胀节导流筒因高温烟气长时间冲刷,导致焊缝开裂移位,破损碎片进入烟机致使振动异常升高联锁停机,停机联锁启动反应进料自保,装置停工。
针对该问题,可采取以下应对措施:1)对高温膨胀节内部进行焊缝着色检查、硬度检查;2)细化膨胀节的检查要求,明确高温膨胀节的检查部位及要求,并根据检查情况进行检修和更换2.2 高温烟道及膨胀节应力开裂2.2.1 再生烟气控制阀后焊缝开裂
2018年7月17日,J公司1号催化裂化装置因再生烟气DN250控制阀后管道开裂停工处理再生烟气2条分支烟道规格分别为DN250、DN300,装置运行工况下,DN300控制阀保持全开,DN250控制阀开度约为30%。
烟气流量差异导致两条管线的负荷及温度不同,DN300管道流量大、温度高,受热膨胀量较DN250烟道大,造成DN250控制阀后薄弱的热壁焊缝受拉应力出现裂纹,裂纹快速扩展后开裂针对该问题,可采取以下应对措施:1)将断口处清理干净后组对焊接,焊接完成后用4块竖
筋板进行焊接加固,然后在管道外部用DN500管道包覆,内部填灌刚玉衬里料;2)重新进行管道热应力计算,改进管道设计2.2.2 三旋出口烟道膨胀节焊缝高温应力开裂2019年1月4日,C公司1号催化裂化装置三旋出口烟道垂直段膨胀节与烟道焊缝开裂,停工处理。
开裂的原因主要是:1)烟道及膨胀节长期在高温状态运行,处于300系列不锈钢敏化温度范围,焊缝处材质劣化,韧性下降;2)膨胀节筒节壁厚(20 mm)与烟道壁厚(12 mm)相差较大,对接焊缝处存在应力集中问题;3)烟道整体受力呈三维立体多变形态,热变形产生的应力无法得到很好的释放或缓解。
针对该问题,可采取以下应对措施:1)加强烟道运行温度、压力及三机组轴系振动参数监控,增设定点视频监控强化烟道的运行检查,确保烟道及其支吊架安全运行;2)重新对高温管道进行热应力计算,改进管道设计2.2.3 烟道膨胀节露点腐蚀泄漏。
2018年1月11日,Q公司三旋出口至双动滑阀管路第三道膨胀节波纹管(材质Incoloy825)出现腐蚀穿孔(如图2所示),因高温烟气泄漏量较大,被迫停工处理经检查,该部位的几个膨胀节均有不同程度腐蚀,多发生在下部波底,原因是:1)正常生产时,为保证烟机做功双动滑阀开度较小,烟气流速较低,经过双动滑阀的烟气夹带少量催化剂细粉,经长时间沉积增厚,导致热阻增加,使得管壁温度低于烟气露点温度,烟气中的SO。
2、SO3遇凝结水生成H 2 SO3、H 2 SO4等强酸,形成典型的露点腐蚀环境;2)Incoloy825合金在高温(≥720℃)环境中使用,存在两方面的风险,一是该合金在晶界上析出富Cr的碳化物后,材料脆性增加,二是可能会发生氧化、吸硫反应,在晶界两侧的基体产生贫Cr区。
当膨胀节内部工作介质中的O和S元素达到一定量时,膨胀节表面氧化膜不能阻止O和S元素的渗入,这时膨胀节的晶界基体就会发生氧化、吸硫反应,造成晶界强度应力的不断减弱,同时,在应力作用下高温膨胀节会产生微裂纹,加速了晶界的弱化,最终造成高温波纹管膨胀节的失效开裂。
【2】。膨胀节波纹管腐蚀穿孔如图2(a)~图2(b)所示。
图2 膨胀节波纹管腐蚀穿孔采取以下应对措施:1)对泄漏膨胀节带压堵漏;2)将波纹管材质由Incoloy825升级为Inconel625,以增加抗腐蚀能力;3)对波纹管外表面进行全面保温,防止内表面出现露点腐蚀
【3】。2.3 低温部位腐蚀泄漏2020年2月27日,S公司重油催化装置分馏塔顶循抽出管线弯头下部外侧管道(材质20号钢)与支架连接处发生泄漏着火。泄漏处宏观形貌如图3(a)~图3(b)所示。
图3 分馏塔顶循抽出管线腐蚀部位宏观形貌发生腐蚀的主要原因分析如下:1)塔顶含S污水中NH 3-N含量为1 800 mg/L,以Cl-含量2 mg/L估算,塔顶NH 4 Cl结晶温度为116.5℃,比塔顶操作温度高2℃,因此,分馏塔顶部铵盐结晶风险较高。
2)根据分馏塔操作条件和塔顶气相组成,计算得到自然水露点温度为98℃,中国石化《炼油工艺防腐蚀管理规定》建议控制塔顶内部操作温度应高于水露点温度14℃以上如表2所示,分馏塔顶及顶循抽出操作温度均高于计算自然水温度14℃以上,发生露点腐蚀风险较低。
3)选取泄漏部位前后管路作为研究对象建模,开展流动状态数值模拟计算结果表明:在泄漏区域二次流较多,湍动能较大,促进了外侧区域的物质交换,进而促进了该区域的腐蚀【4】另外,由于管道支架直接焊接于主管道上,加速了该部位与外界的热传导,造成管道局部温度降低,可能促进了该部位铵盐结晶及凝结水产生,从而形成NH。
4 Cl垢下露点腐蚀环境,腐蚀20号钢母材引发腐蚀泄漏。表2 分馏塔顶温度分布
针对该问题,可采取以下应对措施:1)对顶循环管线进行测厚或脉冲涡流扫查,找出腐蚀减薄的重点部位,跟踪监管;2)对管线的保温进行检查整改,保证管线不出现局部冷凝点,同时,采用规范的管线支吊架,防止局部传热导致的温度低点;3)优化操作条件,对装置原料进行严格的质量控制,将S、酸、N、Cl含量控制在工艺指标要求的范围之内,保证各部位操作温度与计算铵盐结晶温度和水露点的温差符合要求。
2.4 特阀故障2018年12月12日,G公司3号催化裂化装置沉降器藏量从正常的25 t快速上升到76.8 t,待生塞阀全开后藏量未见明显下降,反应温度从正常时的508℃下降到482.7℃经调整,催化剂循环及反应温度未见好转,反应温度逐渐下降到460℃,反应低温自保切断进料。
检查发现,塞阀与电液执行机构连接体上的6个M12单头连接螺栓全部断裂,塞阀固定保护套外表面硬质合金涂层有明显脱落,阀套内阀杆空间位置存有催化剂,阀头头部有局部衬里脱落损坏,如图4所示
图4 连接体连接螺栓断裂造成该故障的主要原因是:阀杆部位有催化剂和破损的硬质合金涂层进入,造成塞阀上下开关时阀杆磨损、阻力增加阀体与电液执行机构连接体连接螺栓受力明显增加,塞阀在操作调整过程中开关频繁,造成连接螺栓疲劳断裂、塞阀无法打开,进而导致催化剂循环不畅,装置低温自保。
针对该问题,可采取以下应对措施:1)将塞阀电液执行机构连接体连接螺栓材质由35号钢改为35Cr Mo A,并评估和改进固定保护套表面喷涂硬质合金的施工工艺;2)加强对塞阀、单动滑阀和双动滑阀等特阀的运行维护管理,定期组织对特阀进行联合调试和检查,定期对特阀电液执行机构联接体连接螺栓的紧固情况进行检查和更换。
3 动设备故障分析3.1 叶片断裂3.1.1 烟机动叶片断裂2018年5月17日,B公司催化裂化装置因烟机轴位移超标联锁停机,装置切断进料烟机振动超标的原因是,烟机的动叶片瞬时断裂,导致转子不平衡、轴振动突然增大、烟机轴位移过高联锁停机。
故障发生前,生产操作平稳,主风机组运行正常,各测点振动幅值、频谱、相位均无异常,对于叶片瞬时断裂的突发故障,事先在线监测振动无任何异常先兆针对该问题,可采取以下应对措施:1)对故障烟机转子返厂维修,并对同批次其他叶片进行无损检测;2)采用烟机断叶片早期故障预警技术进行烟机运行监控,有效管控烟机运行风险。
3.1.2 主风机动叶片断裂2018年10月4日G公司3号催化烟机动叶片断裂,2020年7月3日Y公司2号催化烟机动叶片断裂,2020年9月12日L公司2号催化烟机动、静叶片断裂,2020年11月28日B公司催化烟机动、静叶片断裂,2020年12月3日J公司催化烟机动叶片断裂及其他动、静叶片全部受损等,均造成了装置非计划停工。
2020年6~7月中国石化催化裂化装置连续发生3起轴流压缩机叶片断裂故障,尽管没有造成非计划停机,但需特别关注3台机组叶片断裂的直接原因均为疫情期间装置低负荷运行造成叶片根部进气部位受力较大,进而产生高周疲劳所致。
针对该问题,可采取以下应对措施:1)避免低负荷运行工况,调节运行负荷时以静叶角度调节为主,避免采用转速调节,防止改变气流激振频率,激发共振,加速叶片疲劳断裂;2)做好动、静叶片尤其是叶根榫槽部位检测,对含缺陷叶片进行更换。
中国石化通过采取上述措施,发现了3家企业AV80以上机组的多个叶片裂纹缺陷3.2 转子失衡2018年12月7日,D公司催化裂化装置烟机结垢严重,在切换备用主风机过程中,烟机叶片上的部分垢块掉落造成烟机振动瞬间超标,装置紧急停工。
2019年4月15日,A公司1号催化裂化装置烟机联轴器侧振动上升到87μm,烟机轮盘侧振动上涨到72μm,装置停工处理对烟机进行解体检查发现:静叶有结垢现象;动叶叶顶磨损严重,叶根部冲蚀,部分锁紧片冲蚀脱落。
可采取以下应对措施防止烟机结垢:1)优化再生器操作温度、烟机入口粉尘浓度、再生烟气O含量、轮盘冷却蒸汽参数、平衡剂金属含量等工艺操作条件;2)与催化剂供应商共同改进催化剂性质,采用低稀土和P含量、低磨损指数的催化剂;3)改进烟机气动、轮盘冷却、动叶涂层等设计
【5】3.3 不对中2020年5月17日,L公司2号催化裂化装置烟机联轴端振动超标,瞬间振动值达到满量程,触发烟机振动联锁,主风机停机,装置切断进料经分析,8个月前烟机联轴端VT401XY振动值开始升高,并缓慢持续上升,诊断为基础不均匀沉降造成机组轴系不对中,振动超标后,备用主风机不能正常备用,造成装置停工。
采取对轴系进行检查调整、待检修时进行基础加固等措施3.4 机组喘振2018年7月13日,C公司1号催化裂化装置按计划停烟机处理叶片结垢造成的振动大问题,切换主风机过程中,操作人员错误切除了1号主风机逆流保护联锁,随后1号主风机发生喘振,导致动、静叶全部损坏,装置停工。
2020年9月17日,M公司2号催化裂化装置烟机西瓦垂直振动大,计划停机更换转子主风机切换备用机组过程中,风机防喘振放空阀卡涩在仪表专业人员进行维修的过程中,该防喘振放空阀失灵全开,主风机并入两器风量瞬间回零,触发主风流量低低联锁,装置停工。
针对以上问题,重点要做好事故预案,强化操作及检维修人员培训4 结论和建议1)通过对2018~2020年中国石化催化裂化装置企业级以上非计划停工原因进行统计分析发现,超长周期(4~5年)运行情况下,动、静设备原因造成的非计划停工占总数的39.29%。
静设备造成的非计划停工中,低温腐蚀泄漏、高温应力开裂、磨损老化、特阀故障、检维修质量等是主要影响因素;动设备造成的非计划停工中,叶片断裂、不平衡、不对中、喘振等是主要影响因素有针对性地进行设计改进、操作优化、深度检维修等工作,能够保障催化裂化装置的长周期运行。
2)在催化设备的全生命周期管理中,应始终以有效管控风险为核心,以最低可接受风险为底线【6】,坚持运用RBI、RCM、状态监测及腐蚀监检测等在线、离线技术工具和方法,以安全可保障前提下的效益最大化为目标,不断优化设备管理。
(1)加强设计、制造管理加强设计管理和变更管理,对于新、改建装置的设计计算和选材、选型、制造等要严格把关,结合装置的原料、产品及有害介质分布等进行针对性的工艺流程和设备选材、选型优化以及制造把关(2)优化操作运行管理。
摸索最佳操作条件,不断优化工艺运行,在效益最好和设备风险最小之间做好平衡,保证适宜的设备工艺运行环境(3)强化检维修管理要充分考虑5年超长周期对设备可靠性的要求,做好检维修管理,对于影响装置长周期运行的关键部位,如:旋分、翼阀、高温热力管道及膨胀节、外取热器、流化风喷嘴、特阀、大型机组、油浆系统。
【7】等要进行深度检验、检修,必要时可以考虑做好备件(4)构建催化设备可靠性数据库以EM系统为基础,按ISO 14224—2016《石油、石化和天然气工业设备可靠性和维护数据的收集与交换》要求,记录故障部位和现象的详细描述、规范化定义设备故障模式(代码)、故障原因和详细描述、采取的维修方法和详细描述(包括维修方法类型)等内容,并使之符合国际标准规范的模板。
【8】,逐步积累形成符合我国实际情况的设备可靠性数据库通过可靠性理论模型推测关键部件的剩余寿命,为设备及备件检修更换、运行装置风险评估提供依据(5)研发设备早期故障预警技术及系统开发机理和数据驱动的动、静设备早期故障预警模型,构建催化设备早期故障智能预警系统,通过在线获取的工艺、分析化验、腐蚀监测、振动等多源实时数据进行预测运算,实现苛刻工况、复杂运行环境下设备早期故障的准确定位和智能预警,不断提高装置安全运行水平。
活 动 推 荐  fill=%23FFFFFF%3E%3Crect x=249 y=126 width=1 height=1%3E%3C/rect%3E%3C/g%3E%3C/g%3E%3C/svg%3E)  fill=%23FFFFFF%3E%3Crect x=249 y=126 width=1 height=1%3E%3C/rect%3E%3C/g%3E%3C/g%3E%3C/svg%3E)  fill=%23FFFFFF%3E%3Crect x=249 y=126 width=1 height=1%3E%3C/rect%3E%3C/g%3E%3C/g%3E%3C/svg%3E)
http://www.iomtchem.com 为深入学习贯彻党的二十大精神,全面贯彻习近平新时代中国特色社会主义思想,保障国家能源安全,中国石油化工产业将进入发展方式大转型和大重构的时代,产业结构性的大重构将在行业发展的各个方面体现,在当前的大势下,石油化工产业淘汰落后产能、推动产能整合升级已经成为必然,大型化、一体化、规模化、集群化、智能化及绿色低碳必将成为行业未来发展趋势。
未来,中国石化工业需继续淘汰落后产能、优化产业结构、推进科技创新、提升设备可靠性运行,实现做优做强和绿色低碳高质量发展提升石油化工企业设备管理实力和装置检维修水平,全面持续推进石化工业迈向更高质量可持续发展。
为了提高石油化工设备管理工作,提高设备智能化运维和维护检修水平,确保石油化工装置安全、可靠、更长周期运行,在中国石油、中国石化、中国海油、中国中化、国家管网、国家能源、延长及地方油气管网、LNG管网、炼油、石化、煤化工、化工企业设备管理部门的大力支持下,
中国化工学会拟于2024年6月19~21号广东广州继续举办“2024年(第五届)石油化工设备智慧运维与检维修技术大会暨展览会” 大会将紧紧围绕“数字化赋能设备智能运维、全力提升设备预知性检修水平”主题,推广应用新技术、新方法、新成果和新产品,引领行业和企业管理与科技进步,促进石油化工产业及相关设备行业健康、有序、高质量发展。
旨在加强我国石油化工设备管理经验分享与技术交流,促进相关产业、企业管理创新和技术进步,提升设备管理整体水平,助推产业可持续高质量发展 诚邀各油气、LNG、炼油、石化、煤化工、储运罐区、化工生产企业设备管理部门及建安检维修、技术服务、设备供应厂商积极参与。  fill=%23FFFFFF%3E%3Crect x=249 y=126 width=1 height=1%3E%3C/rect%3E%3C/g%3E%3C/g%3E%3C/svg%3E)
主办单位:中国化工学会联合主办:中国机电装备维修与改造技术协会石油石化建安检维修分会 中国国际科技促进会炼油与石化专业委员会中国石油化工集团石油化工设备防腐蚀研究中心 中国石油安全环保技术研究院炼化设备中心
拟邀协办:中国石油炼油化工和新材料分公司 中国石化炼油事业部 中国石化化工事业部 中海石油炼化有限责任公司国家能源集团中国神华煤制油化工有限公司 陕西延长石油(集团)有限责任公司生产经营部中石化广州工程有限公司
中国石化广州分公司 中国石油广东石化分公司 中国石化茂名分公司中科(广东)炼化有限公司 中海油惠州石化有限公司 中海壳牌石油化工有限公司中科(广东)炼化有限公司东兴分部 埃克森美孚(惠州)化工有限公司
巴斯夫一体化基地(广东)有限公司支持单位:中国石油天然气集团有限公司 中国石油化工集团有限公司中国海洋石油集团有限公司 中国中化控股有限责任公司国家石油天然气管网集团有限公司 国家能源投资集团有限责任公司
陕西延长石油(集团)有限责任公司媒体支持:《石油化工设备技术》编辑部 / 《石化技术》编辑部 超级石化公众号 / 炼化及石化下游产业网 《炼油与石化下游产业》编辑部 / 石化设备圈公众号 /炼油与石化下游产业公众号 / 石化缘科技咨询公众号
《石油化工企业设备维护与检修》编辑部 / 油气储运与安环技术公众号 石油化工设备维护与检修网 / 石油化工之家公众号《石油化工腐蚀与防护》编辑部 / 石油化工企业设备维护与检修网公众号
数字化赋能设备智能运维 全力提升设备预知性检修水平会议重点研讨内容1.国内外炼油化工装置大型机组检维修发展现状与展望;2.老旧装置超设计使用年限服役承压设备管理对策与思考;3.石油化工装置机泵在线监测系统、预知性维护技术;
4.基于大数据分析的炼油化工设备管理新技术应用;5.特种机泵:螺杆机、真空压缩机、屏蔽泵等检修运维技术;6.石油化工设备润滑要求、机组润滑系统运行及管理;7.石油化工装置法兰密封结构安装与维修技术;8.炼油化工装置烟气轮机长周期运行管理;
9.石油化工装置腐蚀防护及隔热保温;10.液压工具、法兰扭矩及法兰连接完整性管理;11.风机、离心泵、各类压缩机等大型机组优化增效节能改造;12.石油化工电气、仪表设备全寿命周期管理;13.现场仪表、控制阀、泄压阀、安全阀、阻火器、爆破片、过程分析仪表、DCS、FCS等检修运维技术;
14.石油化工装置隐患治理、泄漏治理,大型在役老旧装置的升级改造;15.大型金属常压储罐、球罐、低温储罐的检测检验标准要求和测漏技术应用,储罐本体、边缘设施防腐蚀技术的方法和应用,罐顶内壁喷涂除锈爬壁机器人,防落底措施与方法;
16.大型装置运维数字化转型、无人化升级方案,巡更机器人、火情侦测与消防机器人、无人机等新型技术的应用;17.可燃、有毒等挥发性气体、挥发性有机物的泄露监测、气体探测传感器的应用;18.露天设施的雷电预警技术、防雷接地技术、静电接地技术应用;
19.新型浮盘及密封安装、检修技术;20.炼油化工装置大型机组核心部件修复再制造;21.新设备、新技术、新材料在石油化工领域的应用会议拟邀请代表中国石化、中国石油、中国海油、国能集团、中化集团、国家管网、陕西延长、民营炼化企业的设备管理与技术人员及工程建设公司、石化设备制造企业、检维修服务企业管理与技术人员和相关技术研究机构、大专院校等单位的科研与技术人员参加会议。  fill=%23FFFFFF%3E%3Crect x=249 y=126 width=1 height=1%3E%3C/rect%3E%3C/g%3E%3C/g%3E%3C/svg%3E)
大会时间安排6月20号:全天开幕式及全体大会,特邀领导、专家主旨演讲;6月21号:全 天分论坛一:炼化企业转动设备管理与检维修技术大会;分论坛二:第二届中国石化罐区系统安全与VOCs治理技术大会;分论坛三:第三届炼化企业过程安全与腐蚀防护技术大会;
分论坛四:石化设备润滑管理与智能润滑技术大会;分论坛五:石化严苛工况阀门运行与检修技术大会;分论坛六:煤化工设备运行管理与检维修技术大会;分论坛七:油气管道管网完整性管理与抢维修技术大会;分论坛八:石化行业智慧运维与智能巡检机器人发展大会;
分论坛九:催化烟气轮机运行管理与检修技术大会;分论坛十:石油化工行业换热设备运行管理与维检修技术大会。咨询:18610555705(微信)
石油化工设备维护与检修网扫码关注我们吧!  fill=%23FFFFFF%3E%3Crect x=249 y=126 width=1 height=1%3E%3C/rect%3E%3C/g%3E%3C/g%3E%3C/svg%3E)  fill=%23FFFFFF%3E%3Crect x=249 y=126 width=1 height=1%3E%3C/rect%3E%3C/g%3E%3C/g%3E%3C/svg%3E)
素材来源:化工技术、由石油化工设备维护与检修网整理免责声明:所载内容来源互联网等公开渠道,我们对文中观点保持中立,仅供参考,交流之目的转载的稿件版权归原作者和机构所有,如有侵权,请联系我们删除点击阅读原文,上石化检修网,了解更多行业资讯。
方钉百科
|